COATINGS
Plasma spray coatings
These coatings are essential for sustainably improving the integration and fixation of the implant in the patient’s body.
The technique relies on spraying metallic or ceramic powder onto the implant using a plasma torch.
Plasma is a term used to describe a gas that has been heated to a sufficient temperature to ionize and become electrically conductive. This gas flow is brought to very high temperature (between 15,000 and 20,000 degrees) by an electric arc between a cathode and an anode. Powder is injected into this gas stream, will melt and transform into fine droplets that deposit on the substrate to be coated.
This type of process makes it possible to obtain a homogeneous coating with good resistance to wear, abrasion and corrosion.
Robotic plasma installations spray metallic powders (titanium, chrome-cobalt) or ceramic (hydroxyapatite, alumina) in single or double layers, under atmospheric conditions (APS) or under vacuum (VPS).
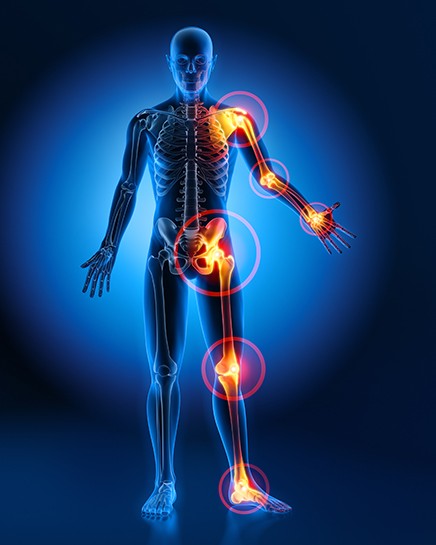
MedicalGroup offers comprehensive expertise and processes, in compliance with the applicable ISO 13779, ISO 13179 and ASTM standards:
- all types of implants (shoulder, hip, knee, extremities, disc, cochlear implant…)
- of all sizes
- on all substrates (titanium, stainless steel, chrome-cobalt)
- with different technologies: atmospheric plasma (APS) or vacuum plasma (VPS)
- by spraying metallic or ceramic coatings, in single or double layers
Part preparation: cleaning, masking, sandblasting
The parts to be coated are first cleaned on an automated cleaning line.
They pass through different baths, whose parameters are strictly controlled.
Parts are masked to expose only the areas to be coated. This masking is done according to our clients’ specifications. It is carried out using adhesive resistant to very high temperatures, medical grade silicone masks or tooling developed according to the part geometry.
Before plasma processing, parts are prepared by abrasive blasting, to guarantee coating adhesion. This sandblasting creates surface roughness on the implant.
The implants are then cleaned and packaged.
Plasma
Robotic plasma installations spray metallic powders (titanium, chrome-cobalt) or ceramic (hydroxyapatite, alumina) in single or double layers, under atmospheric conditions (APS) or under vacuum (VPS).
Plasma cycles run automatically, according to pre-recorded programs and validated parameters.
Once the coating is complete, the parts are unmasked and individually checked.
Metallic coatings are governed by the ISO 13179-1 standard.
Hydroxyapatite coatings are described by the ISO 13779 series standards and the ASTM F1609 standard.
Proper coating control requires compliance with performance requirements on mechanical, chemical and morphological properties. Tests carried out within our Laboratory according to current standards attest to the control and reliability of our processes and allow our clients to perform all product-specific validations necessary for their regulatory files.